Compact Automated Pack and Palletizing Cell Loading Flexible Bags into Cases or Totes
- Application: Automation of the complete end-of-line packaging process for a new line of bagged pesticides into RSC cases and display style pallet size totes
- Speed: 36 products per minute, 7 different product, pack and pallet/gaylord configurations
- ROI Justification: Minimize labor usage for the new line as much as possible
- Unique Challenges: Confined space
- Important to Customer: Confidence in the reliability of the solution, single source supplier for the entire solution
Solved with Pearson’s RPC
Optimized for Demanding 24/7 Operations
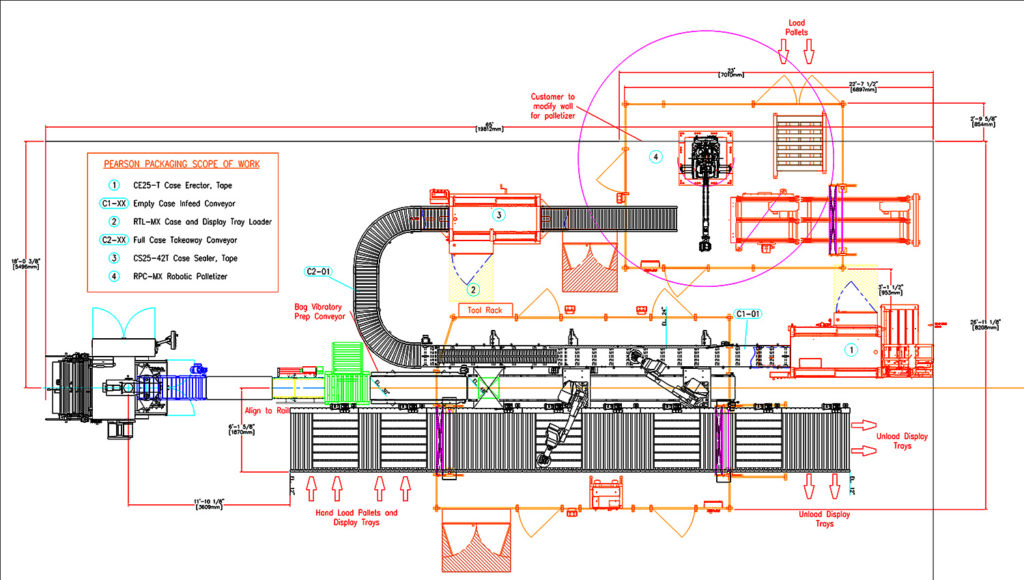
After exploring competitive solutions that were as much as $300,000-400,000 lower, this customer entrusted us with their project to form RSC cases, pack bags into the cases, seal the RSC cases and palletize them. The system also picks and places the full range of bags into a display style totes. The soundness of the following benefits sealed the deal:
- The technical solution workable in a small space
- The ability to source from one supplier offering seamless integration
- A uniform interface for all of the equipment
- One-stop after-sales and technical support
The gusseted and flat bagged products ranging from 3lbs to 20lbs enter the cell in a single row. Vibration settles the product and flattens the bags on their way to the pick belt. Cases leaving the case erector now enter the packing cell and index into the side-belt conveyor to the north of the product conveyor on a repeatable pitch. Bags are picked and the case packing is completed by using the progressive loading methodology that eliminates the need to stop and start cases during the load cycle. Loaded cases are automatically closed and sealed prior to palletization. As cases enter the palletizing cell, they accumulate on a zero-backpressure 24-volt conveyor and are referenced in the pick zone. In the meantime, the robot positions a pallet for loading before picking the case to place onto the pallet according to the recipe. The finished pallet is then conveyed out of the cell through the safety light curtain.
The other operational mode is to pack the totes. Here the operators manually place display style totes onto the buffer conveyor to the south of the product conveyor, where they are automatically indexed into the system. Vision and line tracking communicate the location of the bags and cases to the robot to pick and place the product accurately. Full display style gaylord trays are automatically driven out of the cell, through the safety light curtain, for fork truck pick-up.
RTL-MX Capabilities
- Application: Top Load Case Packing
- Case Support: Chipboard cartons, corrugated cases, bliss boxes, trays, and warehouse totes
- Supported Pack Patterns: Vertical, horizontal, interleaved, stacked, on edge, on end, rainbow or variety packs, bulk and shelf-ready
- Speed: Application specific up to 1,500 products/min
- Controls: FANUC PMC | AB CompactLogix PLC | PanelView Color HMI
- Operation:
- Robotically using multi-axis articulated robot with MTBF of over 80,000 hours and flexibility to accommodate product changes or variations
- Application specific product handling and transfer including servo-collating, diverting, tabletop, mat top and independent cart technology
- Vision guidance and line tracking to inspect, detect, sort and manipulate products on the fly or balance the load between robots
- Continuous case motion design for higher speed applications and reduced wear
- Application-specific end-of-arm tool with optional automatic tool changeover
- Programming Language: PackML
- Safety Guarding: Fencing, light curtains or area sensors
RPC Capabilities
- Application: Palletizing and Depalletizing
- Case Support: Chipboard cartons, corrugated cases, bliss boxes, trays, warehouse totes, bags, bales, pails, drums, bundles, bottles, jugs
- Supported Pallet Patterns: Column-stacked, interlocked or pin-wheel configurations, mixed loads or variable pattern placement programming
- Speed: Slow to medium speed single case and row picks, high-speed full layer picks
- Controls: FANUC PMC | AB CompactLogix PLC | PanelView Color HMI
- Operation:
- Robotically using multi-axis articulated robot with MTBF of over 80,000 hours and flexibility to accommodate product changes or variations
- Accurate sorting of cases from single infeed to multiple outfeeds using barcodes
- Pallet handling using conveyors, transfer carts and automated or autonomous guided vehicles
- Application-specific, multi-functioning end-of-arm tools to pick pallets, cases and slip sheets
- Integration of an automatic pallet dispenser
- Integration of an automatic slip sheet dispenser
- Programming Language: PackML
- Safety Guarding: Fencing, light curtains or area sensors
Minimized Total Cost of Ownership
- Robotic operation takes advantage of high mean between failure of 80,000 hrs, reduced parts count and wear
- Standard remote access capability for efficient technical support and extensive service cost savings
- HMI models web experience for quick familiarity, intuitive operation, reduced training needs and better upkeep of the equipment, pallet selection is recipe driven
- Easy-to-use pallet configuration tool to quickly create, modify, copy or clear recipes on the HMI or adjust parameters such as case or pallet height or number of layers
- Robot Preventative Maintenance Program ensures optimal uptime and controlled parts and service expenses year over year
Interested to learn more about this solution?
Click here to contact us today!