Loading and Unloading of Seafood Pouches into a Retort Tray System
- Application: Loading pouches of seafood into trays in preparation for the retort process, followed by unloading of the sterilized product, the system includes tray handling
- Speed: 25 pouches per minute
- ROI Justification: Lack of available labor and elimination of unproductive operator wait times
- Unique Challenges: Continuous operation and full automation in a small footprint while meeting all safety requirements. The system also needed to include a manual mode for short runs of products.
- Important to Customer: An experienced partner that can provide an engineered solution that fits all needs and is able to support it in the long run
Solved with Pearson’s RTL-MX
Optimized for Demanding 24/7 Operations
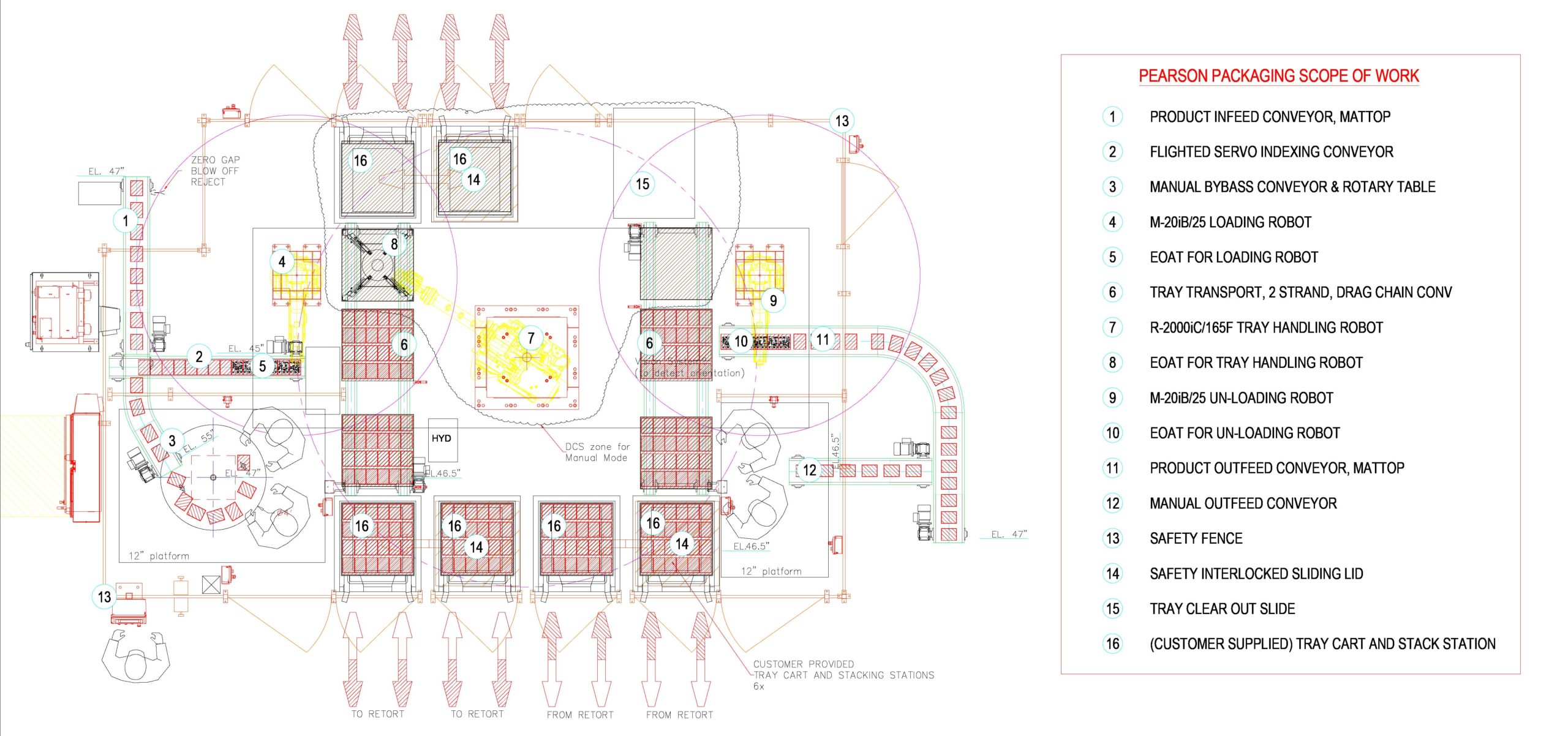
The pouches of seafood are received in a single lane, traveling length parallel to flow. The product enters the Loader/Unloader system onto a straight mat-top conveyor (1) and then jump transfers to a 90-degree, flighted servo indexing conveyor (2). The product is then presented to the loading robot (4) where a full row of 6 pouches is being picked and placed into the available retort tray.
A centrally positioned tray handling robot (7) picks an empty tray from the tray carts (16 north), places it onto the transport conveyor to advance to the pouch loading station (6). Once a tray is fully loaded, the transport conveyor indexes it to the full tray pick area, where the tray handling robot takes it off the conveyor and places it into a retort cart and hydraulic stacker/un-stacker station (16 south). Once the retort cart is full, the safety lid slides over to the second retort cart and an operator removes the full cart to proceed to the retort system.
After completing the retort process, full trays are reintroduced into the system on the unload side. The tray handling robot picks a single full tray from the cart and places it onto the transport conveyor. The full tray then advances to the unloading robot (9) where a full row of 6 pouches is being picked and placed onto the product outfeed conveyor (11). After the tray is fully un-loaded, the tray handling robot picks and inverts it over a cleanout slide (15) and then places it either into one of two stacker/un-stacker stations or back to the loading side depending on availability and process mode.
For short runs, a manual mode disables the loading and un-loading robots, and reduces the tray handing robot’s work envelope to meet RIA safety standards. In this configuration, the tray handling robot only handles the empty trays on the north end of the system away from the manual operations. Incoming pouches are then diverted to a manual bypass conveyor and rotary accumulation table (3), where two operators manually load pouches into the trays and slide the loaded trays into the adjacent stacker station. On the un-loading side, two additional operators slide trays of pouches out of the un-stacker station and manually transfer the product to the manual outfeed bypass conveyor. During the manual loading and unloaded process, empty trays are presented to and removed from the operators via the drag chain tray handling conveyors. The tray handling robot removes and places empty trays at a safe distance from the operators.
RTL-MX Capabilities
- Application: Top Load Case Packing
- Case Support: Chipboard Cartons, Corrugated Cases, Bliss Boxes, Trays, and Warehouse Totes
- Supported Pack Patterns: Vertical, Horizontal, Interleaved, Stacked, On Edge, On End, Rainbow or Variety Packs, Bulk and Shelf-Ready
- Speed: Application specific up to 1,500 products/min
- Controls: FANUC PMC | AB CompactLogix PLC | PanelView Color HMI
- Operation:
- Robotically using multi-axis articulated robot with MTBF of over 80,000 hours and flexibility to accommodate product changes or variations
- Application specific product handling and transfer including servo-collating, diverting, tabletop, mat top and independent cart technology
- Vision guidance and line tracking to inspect, detect, sort and manipulate products on the fly or balance the load between robots
- Continuous case motion design for higher speed applications and reduced wear
- Application-specific end-of-arm tool with optional automatic tool changeover
- Programming Language: PackML
Minimized Total Cost of Ownership
- Robotic Operation takes advantage of high mean between failure of 80,000 hrs, reduced parts count and wear
- Standard remote access capability for efficient technical support and extensive service cost savings
- HMI models web experience for quick familiarity, intuitive operation, reduced training needs and better upkeep of the equipment
- Tune-Up Plus Program ensures optimal uptime and controlled parts and service expenses year over year
Interested to learn more about this solution?
Click here to contact us today!